By Mengjie (Jessie) Jiang
The latest purchase of Atlas Tool & Die Works Inc. is a high-tech machine called a “vertical machining center” that processes parts with complex profiled surfaces in single setups. The company’s Lyons factory was built on manual work nearly 100 years ago, and Atlas has participated firsthand in manufacturing’s continuing evolution toward more and more automation.
Zach Mottl, the fourth-generation owner of Atlas, said the current trend is to combine things that used to be done by separate operations into one. “The advances that I’ve been seeing primarily are putting more features, more technology, more precision, more automation on some of the existing technologies,” Mottl said.
Manufacturing still plays a significant role in the U.S. economy, accounting for 12.1 percent of GDP and 9 percent of the workforce in 2015, according to the Bureau of Economic Analysis. For every $1 spent in manufacturing, $1.81 is added to the economy, and for every one worker in manufacturing, there are another four employees hired elsewhere.
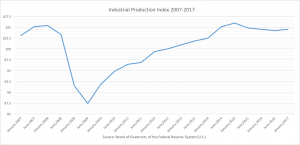
The common notion that manufacturing in the United States is in decline is factually incorrect. Manufacturers contributed $2.17 trillion to the U.S. economy in 2015, having risen from $1.70 trillion in recessionary 2009, according to the National Association of Manufacturers. Boosted by stronger orders and production, the Institute for Supply Management’s manufacturing index for February 2017 climbed to 57.7, the sixth straight advance and the highest since August 2014.
The continued growth of manufacturing is primarily due to the growth in productivity of production processes. According to the U.S. Bureau of Economic Analysis, the annual output per worker for all manufacturing was $149,299 in 2012, a 90 percent growth from 1998, with the highest improvement, 829 percent, in the production of computer and electronic products, and double-digit growth in automobiles, transportation equipment, miscellaneous products, primary metals machinery, electrical equipment and food.
The production improvement plays a significant role in the change of manufacturing employment. A report released by Ball State University in 2015 attributed almost 88 percent of manufacturing job losses in recent years to enhanced productivity because of technology advancement and the rest to trade and changes in domestic demand for goods. Growing demand for manufactured goods in the U.S. has offset some of the job losses, but the affect is modest, accounting for a 1.2 percent increase in jobs.
Take the manufacturing in the Chicago region. Metropolitan Chicago is home to more than 360,000 manufacturing jobs, accounting for over 60 percent of Illinois’s manufacturing employment, according to a recent report by the Chicago Metropolitan Agency for Planning. From 2001 to 2016, the Chicago region lost approximately 30 percent of 170,000 manufacturing jobs, while output increased by nearly 5 percent in the same time period, hitting an all-time high of $74.8 billion in 2015.
“It’s a trend and there is still no doubt about that. The ability for machines to do what people used to do has increased tremendously over the last 30 to 40 years and will continue to increase,” said Greg Baise, president and CEO of the Illinois Manufacturers’ Association.
Around 50 percent of all the activities people are paid to do in the world’s workforce could potentially be automated, which amounts to nearly $15 trillion in wages, according to a report in January by consultancy McKinsey & Co. The activities most likely to be automated, the report stated, are physical ones in highly structured and predictable environments, as well as data collection and processing. In the U.S., manufacturing, accommodation and food services, and retail trade are among the most susceptible to automation.
However, the report declares that, that given current technologies, less than 5 percent of occupations can be fully automated, and elsewhere automation is more a supplement to human workers.
“Most of the systems or programming and hardware we are working with, we are not working from the ground up, we are using tools that kind of get you 50 percent there,” said Andrew Griesemer, a system engineer at engineering consulting company DMC Inc. “That’s why this job is sometimes referred to as an integrator, as there are a lot of tools out there that do the low level things and it’s our job to combine those. As the level of complexity goes up, so does the sophistication of the tools.”
Griesemer foresees the possibility of small machines monitoring the performance of the larger, production machines.
“Everything is now connected to the Internet. Within the automation space, they are adding more sensors on there that can track of the performance of these machines, and people are now doing is kind of gathering high level data on their higher operation to be able to figure out some of the business side, how these machines are running,” Griesemer said.
Automation is also taking human operators from potentially unsafe operation.
Brain Greviskes, president and CEO of Compass Automation Inc., said the newest technologies are collaborative robots which can almost understand their people process and prevent workers from being hurt while walking into the equipment, and there’s a feedback mechanism internal to the robots that can force them to stop if they bump into a person.
Automation is also stepping into the medical device industry with what’s called “an evolved vision system” to improve the products. “We’ve developed a vision system for some of our surgical implant manufacturers that actually go and measure the surgical implant at the level of microns, so we know how precisely these parts are being manufactured, and they have to be manufactured extremely precisely as they are used in human bodies,” Greviskes said.
Despite the advantages of automation, its pace and extent depend on the cost of technology and labor including skills and supply and demand dynamics.
Asked about the considerations in adopting a new machine, Mottl said, “I look for some type of market demand, or either now I have potential orders from my current customers, or I see I can get new customers if I have this new technology, and I look at the cost of technology and the risks.”
While automation has displaced jobs, it has created new ones over time as an increase in automation reduces the cost of producing using labor, and thus discourages further automation and restores the labor share and employment back to their initial level, M.I.T. research found.
However, there is an inequality during the transition as high-skill labor has a comparative advantage in producing the new complex tasks. In January, unemployment was 2.5 percent among adults with bachelor’s degree and higher, comparing with 5.3 percent among adults with only a high-school diploma, according to the United States Department of Labor.
“Ten years ago if you ask me if computer skills were important on my production crew, I would tell you no, but now computer skills are really important,” Mottl said. “If they don’t know how to log into the computer terminal and input data, they can’t even run a punch press.”
The manufacturing industry has witnessed a yawning gap between job openings and job hires. About 42 percent of 136,000 manufacturing job openings went unfilled in December 2016, versus 26 percent in the previous month, according to the Labor Department.
Baise, of the Illinois Manufacturers’ Asssociation, called for more resources for workforce development programs to help young people get the certifications necessary to work at today’s manufacturing facilities.
“There needs to a general understanding that manufacturing provides good, middle-class jobs, and it’s a good, long-term career to get involved in it, so society in general should be supportive of that,” Baise said.